
The fire-resistance rating is expressed by the number of hours that the assembly can maintain its integrity while containing gases and excessive temperature increases out of the fire compartment. In the United States, the assemblies are required to be “fire-rated” (IBC ) based on their ability to withstand a standardized “fire” test (ASTM ).


In a fire, partition walls serve as primary barriers to maintain building integrity, and avoid the spread of fire between compartments (rooms). CFS interior partition walls are framed with studs, have track at top and bottom, and are then sheathed (most commonly) with gypsum wallboard(s). CFS stud and track are used extensively in buildings as the framing for interior partition walls, exterior curtain walls, and more recently as the complete load-bearing system (Allen, Schafer ). The most common members are channels (tracks) and lipped channels (studs and joists). The review provided here includes experimental results on mechanical and thermal properties of cold-formed steel and temperature dependent constitutive relations, subsystem testing and computational simulations, and analysis models and exploratory methods for fire design, i.e., the building blocks towards performance-based fire design for cold-formed steel systems.Ĭold-formed steel (CFS) members are manufactured from cold bent sheet steel, approximately from 0.5 mm to 3.0 mm thick. Today, engineering knowledge is rapidly advancing, providing the opportunity to contemplate analysis-based design as an enabling tool for general performance-based fire engineering of cold-formed steel systems. However, in fires the performance of cold-formed steel systems are assured by prescriptive detailing and standardized testing. Consequently, design specifications, and structural analysis tools have rapidly evolved to facilitate engineering design of these complex thin-walled members. Cold-formed steel systems have become popular in building construction as both load-bearing and non-load-bearing elements, primarily due to their high strength-to-weight ratio and ease of construction. This paper brings together existing research on cold-formed steel materials, members, and assemblages at elevated temperatures and complementary analysis and design methods necessary for the development of analysis-based design for cold-formed steel systems under fire.

The installation team can build up to 6,000 square feet per week using only a 9-person crew.Performance-based fire design for cold-formed steel systems is in its infancy. Using prefabricated panels means there is less material waste and manpower on the job site. The unloaded truck then departs, and a new truck immediately assumes the unloading position, allowing for continuous wall panel construction without the need for extensive material storage space. For the panels, an on-site area where the wall panel trucks can pull-in, and drop off the trailer is needed.Īs soon as panel trucks arrive on site, a crane offloads the panels and sets the panels in sequence on the structure. Only a 20’x30’ space is needed to lay down the materials, which are the joists and decking for the flooring system. There is a significant reduction in the size of the lay-down area required for the material. Every delivery includes the flooring system components. Once arriving onsite, just in time deliveries greatly benefit the crew. If the onsite team is new to prefabrication and CFS, All Steel provides one of their experts to educate on the installation to ensure the project goes smoothly. Below is the step by step All Steel process and advantages of selecting All Steel’s team of experts for your next CFS project.Īn Installation Quicker Than Any Other You’ve Done
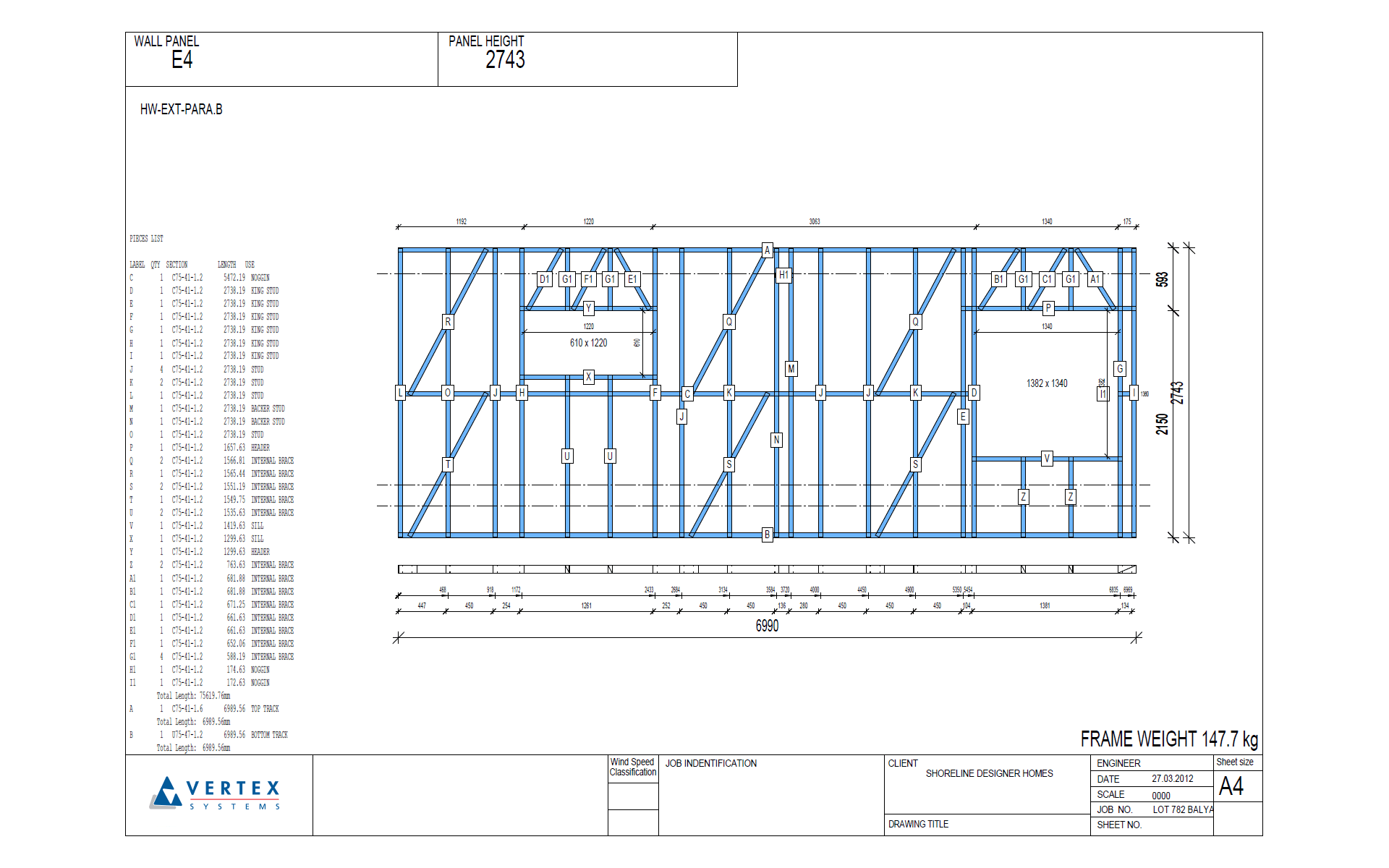
Over this time the team has created a manufacturing process that brings measurable value to all key partners on the mid-rise project team. The team at All Steel Mid-Rise are experts in cold-formed steel framing and panelized systems through a combined over 40 years of experience. The manufacturing process also lends itself to calculated tracking allowing for accurate scheduling, planning and reduced budget. The manufacturing process of framing and panelized systems allows for uniform quality and consistency. Further advancements in the construction industry including the use of panelized systems have made the application of cold-formed steel framing more prevalent. These characteristics have made CFS framing popular amongst owners, developers and contractors to build mid-rise projects more effectively than ever before. Cold-formed steel (CFS) framing is lightweight, durable, noncombustible, and has a strong strength to weight ratio.
